Print and pray: Debug della stampa 3D
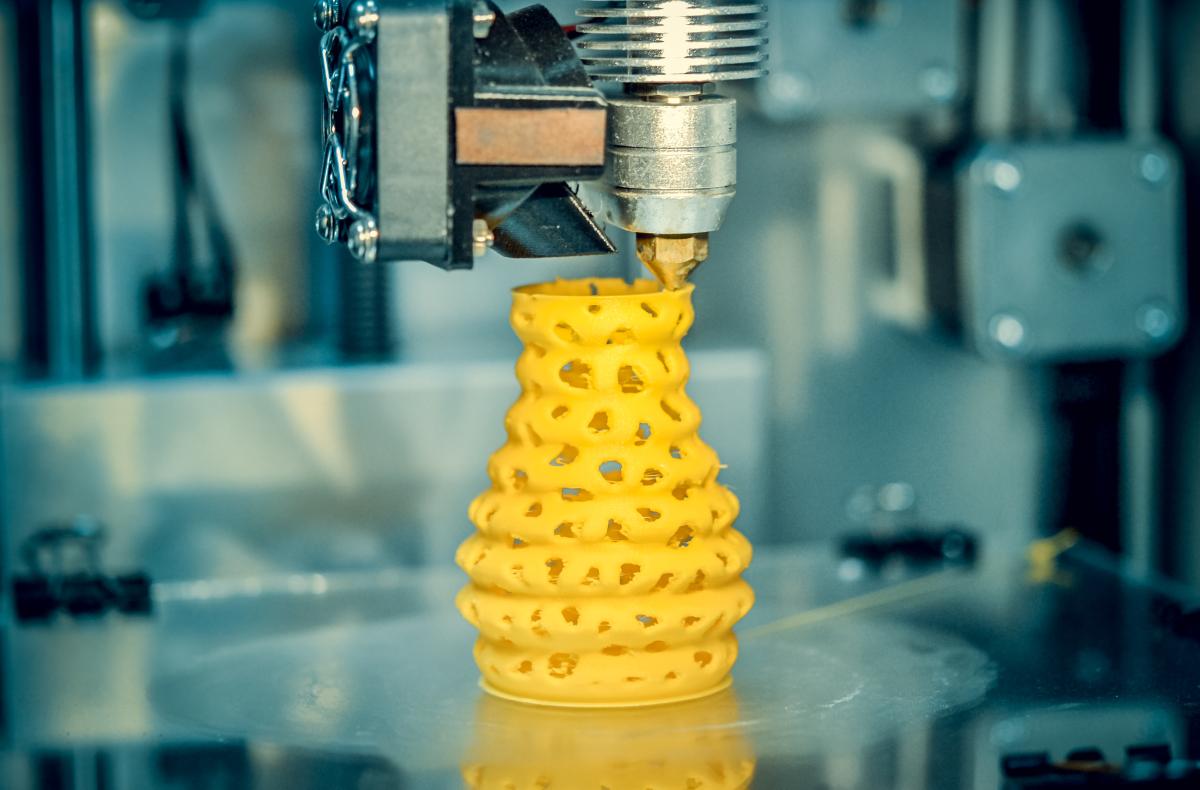
Fuori dal set fantascientifico e direttamente su migliaia di scrivanie? I replicatori di Star Trek sono tra le tecnologie di fantasia più ambite che siano mai state immaginate e, in poco più di un decennio, le stampanti 3D hanno fatto un forte tentativo di portare quell'idea nella realtà. Mentre gli hobbisti sfornano i loro modelli dell'Enterprise (e altri oggetti più utili), la produzione additiva più sofisticata sta rivoluzionando i processi industriali e intere catene del valore. Tuttavia, sia per gli utenti privati che per quelli professionali, il processo di stampa rimane pieno di frustrazioni.
"Print and pray" (stampa e prega) è il motto non ufficiale della modellazione a deposizione fusa (il termine più preciso per ciò che è comunemente noto come stampa 3D): gli utenti si limitano a stampare e a pregare che funzioni. Il ricercatore di NCCR Automation Xavier Guidetti fa un paragone: "Immaginate di voler fare il pane. Non avete una ricetta, sapete solo che dovete mescolare acqua, farina, sale e lievito. Ma nessuno vi dà indicazioni. Sarà un processo penosamente lungo, fatto di tentativi e tentativi, e continuerete a ottenere risultati che non hanno senso per voi".
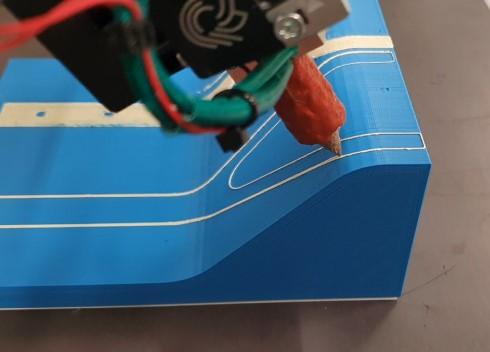
Nel caso della stampa 3D, gli utenti possono disporre di un file di progetto, ma devono comunque cercare di capire tutto, dalla temperatura alle dimensioni delle linee da stampare. Per passare da un progetto a un modello di successo possono essere necessari molti tentativi falliti prima che le cose funzionino come previsto. "Molte aziende che utilizzano le stampanti 3D hanno una persona che è l'esperto e che si dedica costantemente ad assicurarsi che funzioni. Noi vogliamo passare a un software che lo faccia per voi".
Il progetto di Xavier è nato da una conversazione con un amico di un amico - uno scienziato dei materiali, Yannick Nagel, che ha chiesto aiuto per alcuni problemi che stava avendo con un nuovo materiale di stampa. Il progetto si è trasformato in una collaborazione tra studenti, che alla fine li ha portati a continuare a lavorare insieme e a studiare come migliorare la tecnologia di modellazione della deposizione, con il finanziamento di Innosuisse. Altri ricercatori si sono uniti al team, combinando le competenze hardware con quelle matematiche e consentendo di ottimizzare il processo da entrambi i punti di vista. Il punto di forza del team, dice Xavier, è che non si limita a riunire gli specialisti di ogni parte, ma unisce un gruppo di persone che possiedono individualmente una simile gamma di conoscenze. Ciò significa che ognuno di loro comprende appieno il processo su cui sta lavorando.
Chiudere il ciclo di feedback
"Abbiamo affrontato i problemi da molte direzioni diverse", dice."La prima era quella di rendere i pezzi stampati il più resistenti possibile, ma poi, man mano che procedevamo, abbiamo trovato tutti questi altri problemi.Sapevamo come stampare pezzi resistenti, ma non riuscivamo a stamparli in modo affidabile, quindi abbiamo cercato di risolvere quel problema. E poi è emerso un altro problema.Così abbiamo finito per creare una cassetta degli attrezzi con molte soluzioni diverse".
L'affidabilità è comunque il problema principale, che ci riporta all'attuale approccio "stampa e prega".
"Al momento, la stampa 3D è un processo completamente aperto", afferma Xavier."Non c'è alcun tipo di feedback. Non si effettuano misurazioni. Si spera solo che la macchina faccia ciò che ci si aspetta".
Non è affatto soddisfacente. Il team di Xavier ha invece sviluppato una serie di strumenti che includono sensori per misurazioni in tempo reale e controlli algoritmici, che consentono il monitoraggio continuo e la calibrazione automatica. La creazione di un ciclo di feedback chiuso consente non solo una stampa più affidabile, ma anche prestazioni molto più elevate.

Avendo sviluppato e dimostrato una soluzione potente e di ampia applicabilità, il team sta ora lavorando per il lancio del prodotto. Xavier ha recentemente partecipato al workshop sull'imprenditorialità di Bench2Biz, che ha contribuito a definire il percorso da seguire e a identificare il cliente target. Con gli occhi ben puntati sulla commercializzazione, tra qualche anno gli utenti di stampanti 3D potranno finalmente premere il pulsante e saltare la preghiera.
Per saperne di più