On track for better passenger comfort

Anyone who knows what it’s like to ride the London Underground in summer will have a special appreciation for Switzerland’s trains. Not only are they frequent, punctual and rarely overcrowded, but they maintain a comfortable temperature! Whatever the season, you won’t arrive at your destination either bathed in sweat or shivering. And considering the frequent changes on board – sudden crowds getting on or off, clouds parting to send sunbeams right through the windows – that’s no small feat.
But achieving this level of comfort requires a lot of energy input. The sophisticated heating, ventilation and air conditioning (HVAC) system is, after traction, the biggest user of energy on SBB trains. Of course, that means improving efficiency here can make a significant contribution to overall energy savings, and that’s where Ahmed Aboudania is focusing his efforts.
The key is using the latest control methods to improve the automated activation of heating and cooling. In collaboration with SBB, Ahmed has been developing a solution using model predictive control (MPC), which excels at optimising within set constraints and, crucially, can take account of expected as well as current conditions.
At present, the HVAC system supplies fresh air to the train and maintains the internal temperature with a two-part controller. First, a rules-based controller determines the target temperature within the train, guided by European standards. This controller then sends instructions to a proportional integral derivative controller (PID), which calculates the difference between the actual and desired temperatures, and adjusts heating or air conditioning output as needed.
Because the controller is constantly measuring actual conditions against the target, and because conditions are constantly in flux, it is constantly adjusting the temperature in response to changes that have already occurred. If the train empties out at one station, then fills up at the next, that might mean the heating kicks in only to cut out again a few minutes later – the controller isn’t able to factor in future information. Besides being inefficient, this can mean a less comfortable ride for the passengers; a steady temperature, and a minimum of airflow, is usually preferable to frequent changes.
Ahmed’s solution is to plug an MPC controller into the existing control system, modifying the desired reference temperature generated by the rule-based controller in line with additional information about weather, occupancy and so on. The MPC then outputs a new reference temperature as input for the PID.
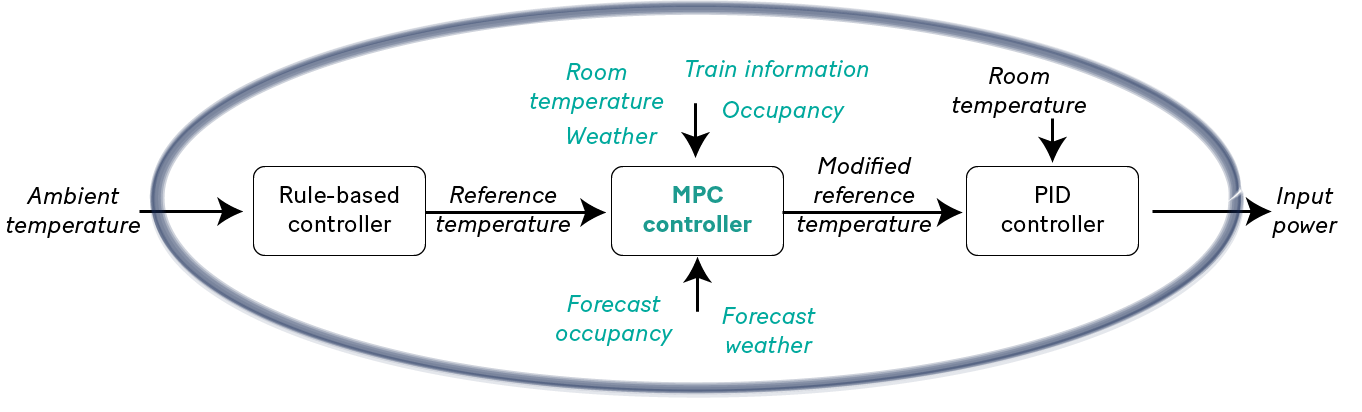
The cheaper and better system
The difference is that the PID is now chasing a more relevant goal, based on a fuller picture of train conditions as well as cost constraints. The MPC takes predicted conditions into account (from the occupancy levels expected after the next stop, to forecast weather changes). Besides that, while PID acts only to control the train climate, MPC can optimise for costs as well as desired temperature. And the MPC targets a narrow temperature range (such as 21-23º), whereas PID always aims for the midpoint (22º). MPC can also control the speed of changes, and consider operational constraints such as maximum input power, improving both comfort and efficiency.
That’s the theory. Ahmed’s team has been working with SBB to put it to the test, by gathering all the necessary data, studying the thermal dynamics of trains (using system identification and machine learning techniques), creating an accurate thermal model (which must be highly precise, but still simple enough to use), and finally running extensive simulations to evaluate the MPC’s performance.
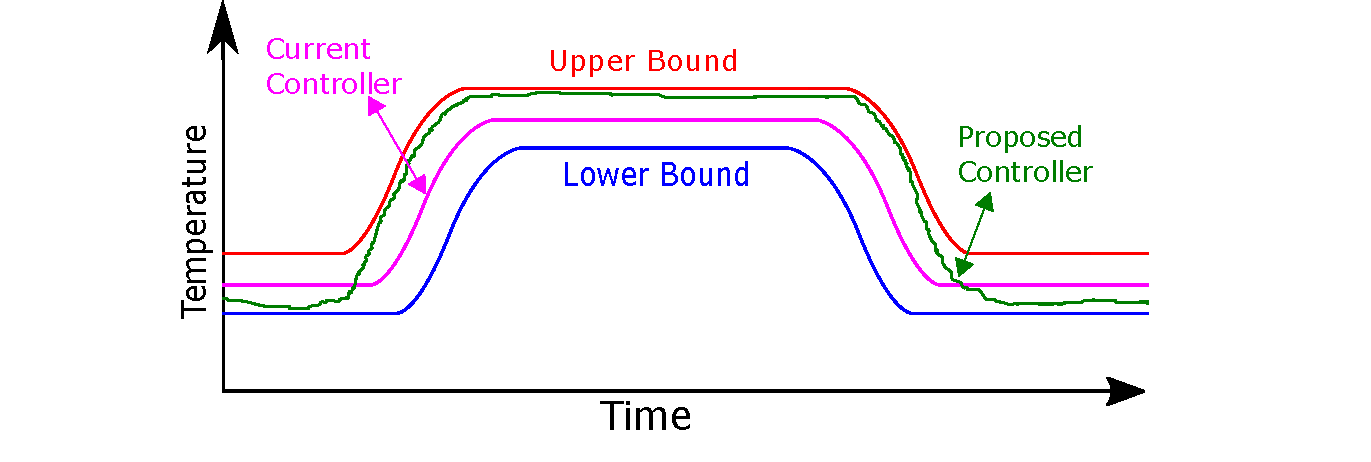
The result? Actual achieved temperatures tend to float at the top or bottom of the allowed band, without breaching it. That means significantly less energy expenditure, since the system minimises compensation for external conditions. In fact, the simulation shows savings of 10% using the MPC – a substantial improvement.
Destination: a transformed fleet?
With the simulation showing such good results, SBB is ready to move further toward implementation. In principle, adopting the MPC should be a far more cost-effective route to energy savings than the expensive and laborious task of retrofitting trains with new HVAC equipment. Once the code is developed, it can easily be rolled out across the entire fleet.

But there are still a number of further stops along the way. The controller must be tested on a real train to see how it copes with challenges such as unreliable weather and occupancy forecasts, communications failures, sensor noise and more.
On top of that, designing the software architecture to build the MPC into the SBB’s secure systems will be a major project in itself. It will mean integrating the controller into a complex network of interconnected but separate elements, and of course achieving safety certification. Security and reliability are naturally higher priorities than innovation for its own sake.
So there are good reasons to travel slowly toward the end goal; but the goal is worth taking time over. Since the total HVAC cost makes up 15-20% of the fleet’s total energy consumption, this makes for a significant environmental benefit, as well as economic. It’s a great example of how NCCR Automation research can bring concrete benefits to Swiss society as well as advancing the state of knowledge.