Print, don’t pray: Debugging 3d printing
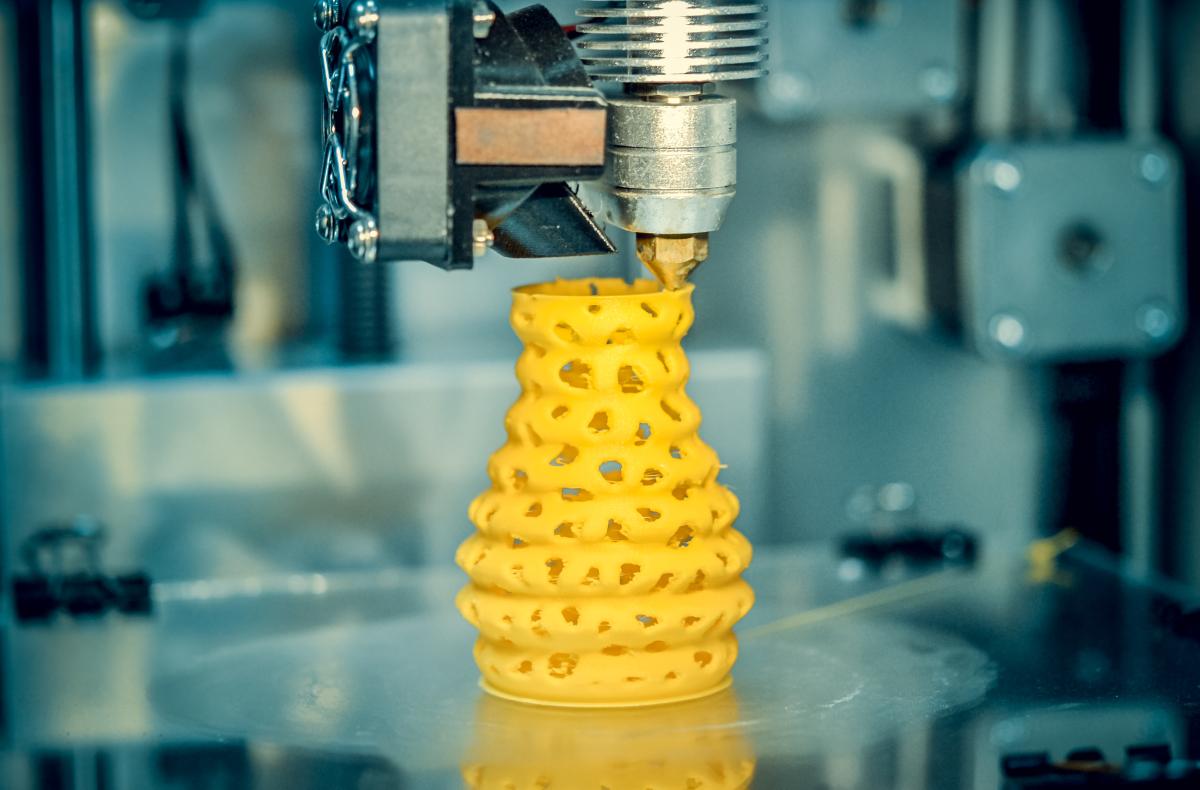
Off the sci-fi set and straight onto thousands of desks? Star Trek’s replicators rank among the most coveted fantasy technologies ever imagined, and in little over a decade, 3D printers have made a strong bid to bring that idea into reality. While hobbyists are churning out their own models of the Enterprise (as well as more useful items), more sophisticated additive manufacturing is revolutionising industrial processes and entire value chains. But, for home and professional users alike, the actual printing process remains riddled with frustration.
“Print and pray” is the unofficial motto of fused deposition modelling (the more accurate term for what is commonly known as 3D printing) – meaning, users just hit print and pray that it works. NCCR Automation researcher Xavier Guidetti draws a comparison: “Imagine that you want to bake bread. You don’t have a recipe, you just know that you need to mix water, flour, salt and yeast. But nobody gives you directions. It’s going to be a painfully long process of trying and trying, and you’ll keep getting results that make no sense to you.”
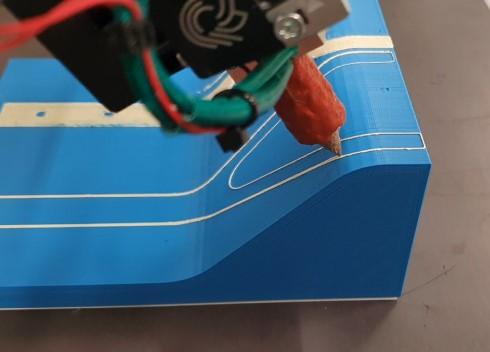
In the case of 3D printing, users may have a design file but they still have to try to figure out everything from the temperature to the size of the lines to be printed. Getting from design to a successful model may require many failed attempts before things work as intended. “Many companies that use 3D printers now have one person who is the expert, and who is dedicated to constantly making sure that it works. We want to move from that to software that does it for you.”
Xavier’s project originated with a conversation with a friend of a friend – a materials scientist, Yannick Nagel, who reached out for help with some problems he was having with a new printing material. This turned into a student project collaboration, which ultimately led them to continue working together and investigating how to improve deposition modelling technology, with Innosuisse funding. More researchers have joined the team, combining hardware expertise with mathematics and enabling them to optimise the process from both ends. The team’s particular strength, says Xavier, is that it doesn’t just bring together specialists on each side, but rather unites a group of people who each individually have that range of knowledge. That means that every one of them fully understands the process that they are working on.
Closing the feedback loop
“We’ve tackled the problems from many different directions,” he says. “The first one was making the printed parts as strong as possible, but then as we progressed, we found all these other problems. We knew how to print strong parts, but we couldn’t print them reliably, so we tried to fix that problem. And then another problem would surface. So we wound up creating a toolbox of many different solutions.”
Reliability is the core issue, though, taking us back to the current “print and pray” approach.
“As of now, 3D printing is really a completely open-loop process,” says Xavier. “There’s no feedback whatsoever. There’s no measurement being done. You just hope that the machine will do what you expect.”
It’s less than satisfactory. Instead, Xavier’s team has developed a toolbox that includes sensors for real-time measurements as well as algorithmic controls, enabling continuous monitoring and automatic calibration. Creating a closed feedback loop enables not only more reliable printing, but far higher performance.

Having developed and demonstrated a powerful solution with wide applicability, the team is now working towards a product launch. Xavier recently took part in the Bench2Biz entrepreneurship workshop, which helped to define the path ahead and identify the target customer. With his sights firmly set on commercialization, in a few years, 3D printer users may be able to finally hit the button and skip the prayer.
Text: Robynn Weldon
Read more